Engineering students in UW-Stout’s Robotics Lab prepare for careers in automation, manufacturing
- klweber2771
- Oct 31, 2024
- 5 min read
Updated: Nov 24, 2024
Students share hands-on experiences in photo essay
By Abbey Goers, UW-Stout
Menomonie, Wis. – A robotic arm swings across a platform, stops and lowers its wrist to pick up a small wooden block with its vacuum grip. The wrist rises and the arm pivots, stops and lowers again to place the block on top of another, forming the second row of a pyramid.
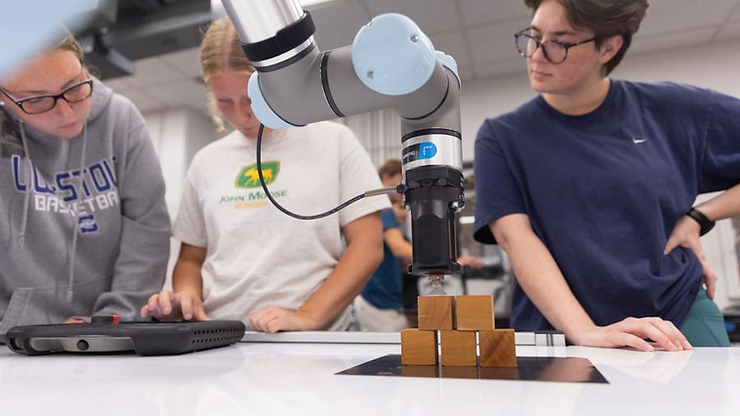
Across the room, other robots are feeding blocks onto conveyor belts or picking up plastic pegs to balance them on top of blocks.
What’s the power behind these small feats of manufacturing engineering? Fourteen teams of two – students in Program Director Paul Craig’s Advanced Industrial Robotics and Vision System Integration course.
Follow the students’ hands-on experiences in robotics and automation in a photo essay.
In UW-Stout’s Robotics Lab, home to more than a half million dollars of equipment, students gain hands-on experience with FANUC LR Mate 200iD robots, designed for assembly, material handling and machine tending; Universal Robot 3e Collaborative robots, compact table-top robots designed for light assembly tasks; and Cognex cameras, a 2D and 3D vision system for machines.

But it all starts in a computer lab in Fryklund Hall, home of the Robert F. Cervenka School of Engineering, where students learn to program the machines, using industry-standard software, like FANUC Roboguide, Universal Robots simulator and Cognex In-Sight Explorer.
On their computer screens, students view digital replicas of what they will see in the Robotics Lab across the hall, where they’ll apply their offline programs in real time.
Craig has instructed engineering courses at UW-Stout for 14 years, continually modifying curriculum to keep his engineering students at the cutting edge of industry practices.

“There’s a lot of material to cover with modules on FANUC robots, Universal Robots, and Cognex vision systems, all running concurrently through the semester. This gives students the most applied engineering experience possible,” he said.
“I have students in manufacturing engineering and engineering technology, and students pursuing dual Bachelor of Science degrees in manufacturing engineering and mechanical engineering.”
In the Robotics Lab, MFGE seniors Aidan Clifford, of Wausau, and Ryan Myers, of Kenosha, work for Craig as lab technicians, assisting their peers in troubleshooting issues in their programs.

At one station, Jackson Majerus and Nathan Notch use a digital Teach Pendant – a tablet similar to a large remote – to set up their program in person on a Universal Robot. They call Myers over for help.
The robot is supposed to pick up a series of blocks and place them on a conveyor belt, one at a time. However, after placing the first block on the belt, the robot swings back to where the first block was, instead of progressing to the second block. The vacuum suction cup grabs nothing but air, before swinging back to lower nothing onto the belt.
“We needed it to run on a pallet-mode, where the robot moves from one block placement to the next. But we had it set on a loop-mode, so it repeated the exact same motion twice,” explained Majerus, of Chaska, Minn.

“The robot will keep doing what it is programmed to do, even if the task is incorrect. It will continue running until it is shut off or reprogrammed correctly. That’s one difference between robotics and AI – robots will not learn from errors,” said Notch, of St. Michael, Minn., who interned at Graco in Rogers, Minn., and Banner Engineering in Plymouth, Minn.
Perfecting a program takes patience. “One program at an internship we were able to run perfectly on the first go. Other runs can take multiple tries, depending on how complex the task is that you need the robot to complete,” he said.
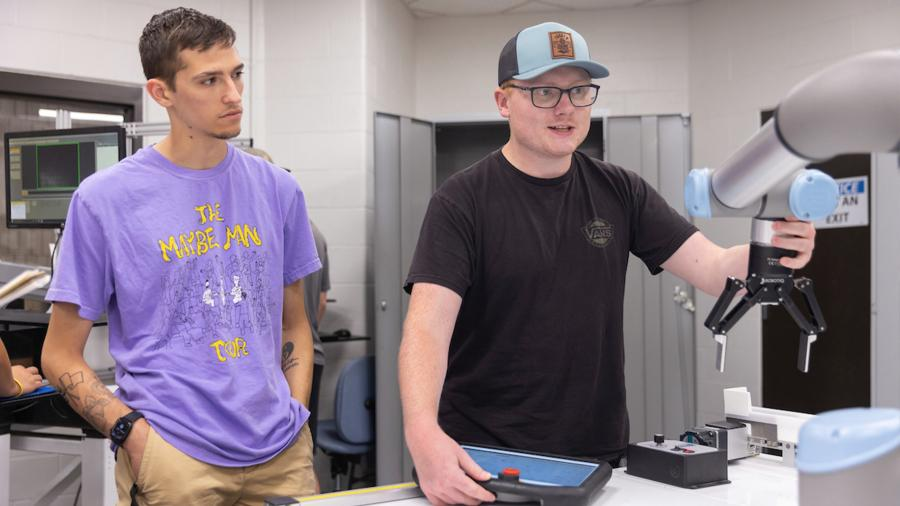
Ben Gurka, of Beloit, and Isaac Shefka, of Appleton, team up at another Universal Robot.
“These applications are helping to get us familiar with the robots used in industry. Universal Robots and FANUC are two of the biggest companies in robotics in manufacturing,” Gurka said, adding that FANUC are used more in heavy automation, while Universal Robots are used in collaborative industries, like packaging.

Gurka used both brands of robots during his internships with plastics fabrication companies – Universal Robots at MacLean-Fogg in Whitewater, and FANUC at Prent Corp. in Janesville.
“The automation saves time and relieves workers of repetitive motions,” he said. He and Shefka would like to develop programs and troubleshoot robotic operations for worker relief and safety, making physical tasks more efficient and less strenuous.

Teams at the Cognex cameras stations help robots “see” what the engineer sees, allowing the machine to identify and inspect parts, measure distances between objects and the area of an object, and correctly position and align objects on a production line, while safely navigating its restricted workspace.
The small cameras are mounted at an adjustable height above a workstation, facing downward to take an accurate image of the desired object – in this case, the wooden blocks.
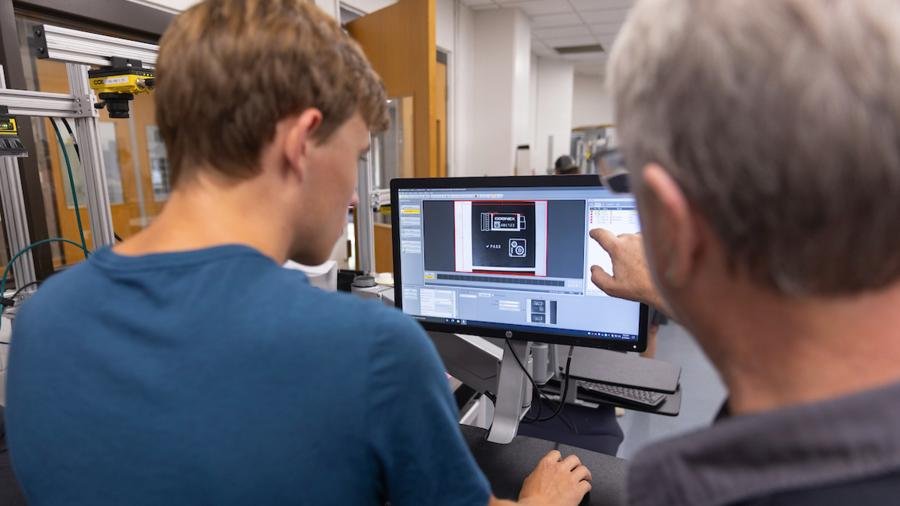
“You upload pictures of the parts you’re working with, giving the camera examples. Eventually, you integrate the vision system with the robot. When mounted to the robot, you can use the live pictures with the software to allow the machine to recognize the parts – you’re teaching the robot what it needs to identify, and the program tells the robot what to do from there,” Clifford explained.
The advanced robotics class builds on an earlier course, where students learn fundamentals of automated manufacturing processes, including developing a palletizing program, a common process used to load items onto a pallet for transportation.
And in a shapes lab, they learn to program a pattern, commanding the FANUC to trace various shapes – the laser pointer in the center of the gripper follows a circle, square and diamond on a black template. Students in the advanced course revisit these skillsets.
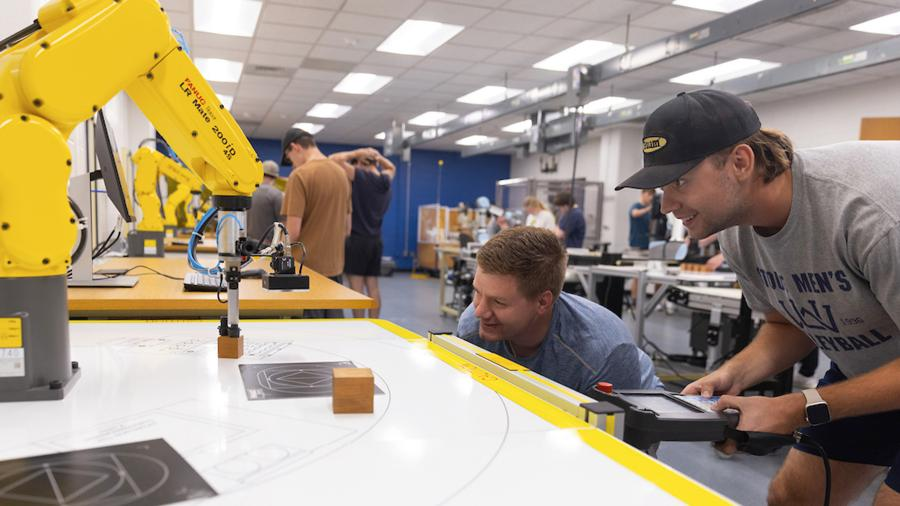
Craig is the 2024-26 Fulton and Edna Holtby Manufacturing Engineering Chair. He uses the professorship funds for “new toys for students, to make them think critically about engineering problems,” he said, including a Cognex snap camera, which is an AI-based camera, plus additional higher-end Cognex cameras for the Robotics Lab.
Craig completed the Universal Robots Teacher Certification Training, which gives him access to core robotics training courses and, in turn, gives his students the opportunity to take a “final exam” to earn an industry equivalent certificate through Universal Robots.
“Having that certification is a great booster to our resumes,” said Shefka, who programmed a FANUC robot to play chess in an earlier course.

UW-Stout’s B.S. manufacturing engineering program is the only undergraduate program of its kind among the Universities of Wisconsin, and one of about 25 in the country. Program graduates are 100% employed within six months of graduation or are continuing their education, as reported in Career Services’ First Destination Report.
UW-Stout’s Robert F. Cervenka School of Engineering, which produces more engineering graduates than any UW university north of Madison, offers undergraduate programs in computer and electrical engineering; engineering technology; mechanical engineering; plastics engineering; and packaging. The M.S. manufacturing engineering degree is available both on campus or online.
A new engineering minor in advanced automation and robotics gives students hands-on experiences with industry-standard manufacturing software, designing and integrating components within complex automation systems, developing techniques in programmable logic control programming, exploring applications in robotic and vision system integration, system security, digital twin technology and more.
Engineering was listed by the Universities of Wisconsin as a key area to address in Wisconsin’s workforce needs in its 2023 workforce proposal.
UW-Stout, a member of the Universities of Wisconsin, is Wisconsin’s Polytechnic University, with a focus on applied learning, collaboration with business and industry, and career outcomes. Learn more via the FOCUS2030 strategic plan.